WELDING INSPECTION, PROCEDURE & QUALIFICATION
The importance of quality welds cannot be overstated; a failed weld can result in serious safety and quality concerns. Because welds encounter loads and fatigue during their lifetime, there is the chance they may fail if not completed to the correct specification for their intended use.
Our certified Welding Inspectors can help your organisation, wherever you are in New Zealand or overseas, with the critical tasks of producing procedures, qualifying welders and inspecting completed welds.
Multiple codes and standards apply to different materials and types of welding to verify the quality and suitability of the welds, together with a welder’s proficiency. Our inspectors interpret and apply these codes to ensure your compliance.
Contact us to find out how our inspectors can help with your business compliance.
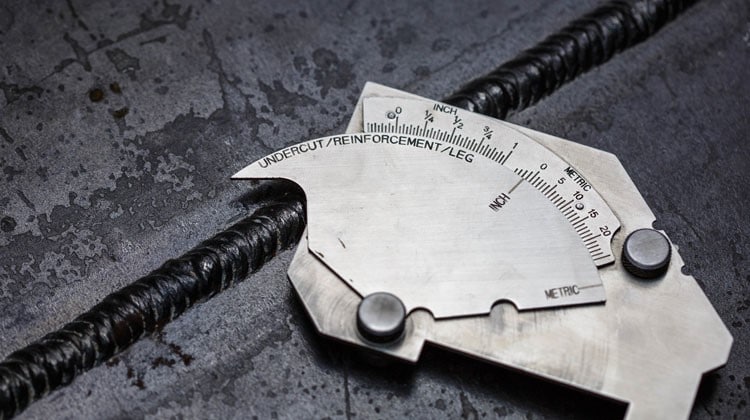
WELDING INSPECTIONS
Methods of weld testing and analysis are divided into destructive (e.g. macro-etch testing, fillet-weld break tests, transverse tension tests, and bend tests) and non-destructive methods (e.g. visual inspection, fluorescent penetrate tests, magnetic particles inspection, eddy current tests and X-rays).
ONE-STOP SHOP
Our inspectors know how to engage in both Destructive and Non-Destructive testing as required and will coordinate with our own mechanical laboratory and NDT team to provide you with a one-stop shop for all your welding inspection requirements.
WELDING PROCEDURE
A Welding Procedure Specification (WPS) is a written document describing welding procedures. It provides direction to the welder for making sound and quality production welds as per the code requirements by giving welders a proof-tested process to follow. A WPS is developed to match the unique combination of material, welding technic, type of joint, welding position and welding consumables used (e.g. wire, rod, shielding gas).
RANGE OF PROCEDURES
Our inspectors can create a WPS for your business that is compliant with AS/NZS 1554, AS/NZS 1665, BS EN ISO 15614 and ASME IX standards.
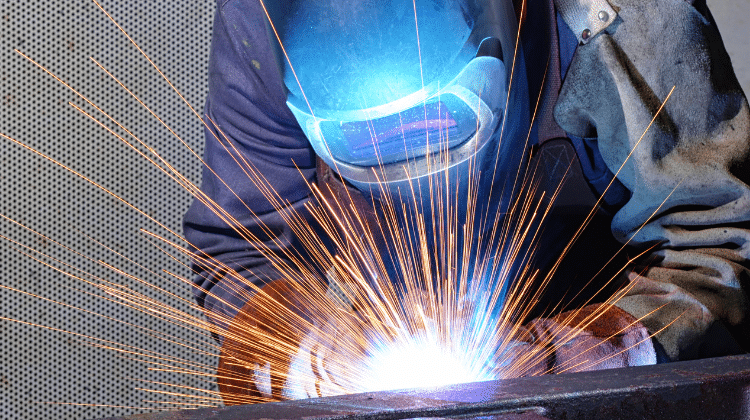
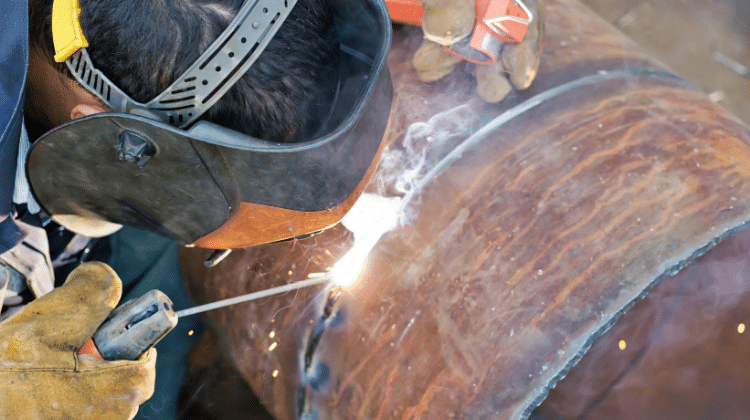
WELDER QUALIFICATION
A WPS is supported by a Procedure Qualification Record (PQR or WPQR). A PQR is a record of a test weld performed and tested to ensure that any procedure used will produce a good weld. Individual welders are certified with a qualification test documented in a Welder Qualification Test Record (WQTR) that shows they have the understanding and demonstrated ability to work within the specified WPS.
RANGE OF QUALIFICATIONS
Our inspectors can issue qualification records compliant with:
- AS/NZS 1665
- AS/NZS 2980-2018
- AS/NZS ISO 9606
- BS EN ISO 9606
- BS EN 287
- ASME IX
QUALITY MANAGEMENT
Under standard AS/NZS 5131:2016 , we provide QA/QC consultancy services.
We assist you during the whole project, from beginning to end, assuring compliance with applicable standards.
During your project we will provide guidance, documentation, and inspections as needed. At the end of the project you will receive a data-book with all the technical information required by the standard.
You won’t need to worry about the quality or compliance of your welding, we will take care of that.
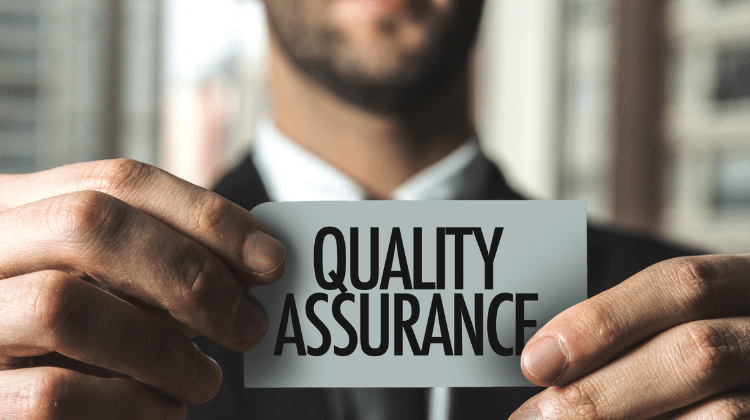
QA/QC SERVICES
- Analysis of scope of work to understand welding requirements
- ITP – Inspection test plan.
- PQR/WPS. (certification and revision)
- Welder qualification (certification and revision)
- Welding preparation
- Materials and welding consumables compliance/ traceability
- Consumable control
- Welding Maps
- Welding Equipment assessment
- Welding inspection before, during and after welding
- NDTs and destructible tests management
- Standard data book release.